G-Splines - Hull form representation with generalized B-spline surfaces

Introduction
The hull form is one of the most important results of the ship design process. A majority of the vessel's properties is dependent on the hull form: resistance, propulsion, power requirement, intactand damaged stability, and last but not least capacities. In addition, the hull form considerably influences the structural design of the vessel, obviously in the case of longitudinal strength, or in thestructural design of complex shaped shell plating.The representation of a hull form in a lines plan is well-known. But how does a computer-based representation work? Even though some hull modeling software still relies on curves, nowadays asurface-based representation of the hull form has become standard. Almost exclusively so-called B-spline surfaces are employed for this purpose. Unfortunately, the kind of B-spline surfaces that iscommonly used causes major difficulties in the context of hull form representation. A hull form is a complex surface, whereas those B-splines are restricted to the simple case of four-sided surfaces. As a consequence, hull forms are composed of several surface patches.The necessity to compose a hull form of several patches has a major drawback. It is necessary to fit neighboring patches continuously to each other, but this is a difficult and time-consuming job.Moreover, it is necessary to maintain smooth transitions between neighboring patches throughout the whole design process, which naturally involves numerous changes of the hull form. As a consequence, hull form modeling is still a laborious task.
Generalized B-spline surfaces
An alternative are generalized B-spline surfaces. The advantage of generalized B-splines is that it is possible to define them on irregular control meshes. Hence, it is possible to represent surfaces ofany complexity with a single B-spline surface. Consequently, the problem to maintain smooth transitions between neighboring patches is omitted.But what is actually the difference between classical and generalized B-spline surfaces? The answer is: only the mathematical approach that is used to construct the surface is different. All theproperties of the resulting surface are equivalent, with just the only exception that irregular control meshes are possible in the latter case. To emphasize this difference, classical B-spline surfaces arededicated to the family of tensor-product surfaces, and generalized B-spline surfaces are dedicated to the family of subdivision surfaces.
Research project
The application of generalized B-spline surfaces in the context of the representation and modeling of hull forms is subject of the research project. So far, the project has shown that the application ofgeneralized B-spline surfaces increases the potential quality of a hull form representation and the modeling of a fair hull form is significantly simplified.Now, the focus of the research project is on the development of appropriate methods to work with generalized B-spline surfaces in hull form design.
Contact: Sebastian Greshake
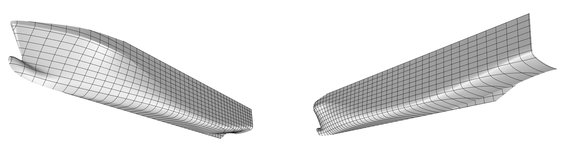